Zinc casting is a manufacturing process that has gained popularity in recent years due to its unique set of advantages. It involves the use of zinc alloys to create various components by injecting molten metal into molds. This process produces high-quality parts that have excellent surface finishes and dimensional accuracy.
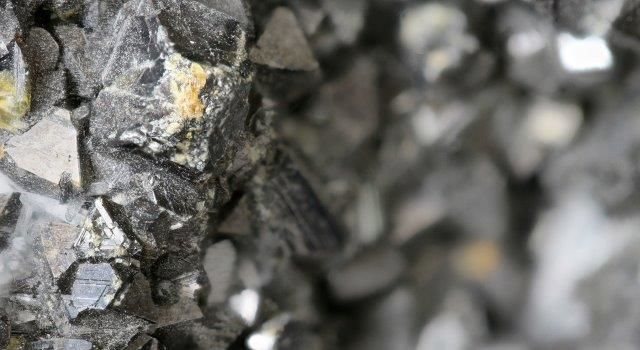
In this blog post, we will explore the benefits of zinc casting, its applications, and how it compares to other casting techniques.
Benefits of Zinc Casting
1. High Strength: Zinc alloys have high strength-to-weight ratios, making them an ideal choice for producing lightweight yet sturdy components.
2. Versatility: Zinc casting can produce a wide range of shapes and sizes, making it an excellent choice for manufacturers that need to create complex, intricate parts that other methods cannot.
3. Corrosion Resistance: Zinc alloys are naturally resistant to corrosion, which makes them ideal for use in harsh environments where corrosion is a problem.
4. Low Cost: Zinc casting is an affordable option as it involves minimal tooling costs, and the process is efficient, allowing for high volume production.
5. Malleability: Zinc alloys are highly malleable, allowing for ease of shaping and production of intricate designs.
Applications of Zinc Casting
The versatility of zinc casting makes it applicable in various industries, including:
1. Automotive: Zinc casting is commonly used in the automotive industry to produce transmission housings, carburettors, and engine parts.
2. Electronics: Zinc casting is the preferred choice in the electronics industry due to its excellent electrical conductivity and heat dissipation capabilities.
3. Medical: Components used in medical devices, such as surgical instruments and diagnostic equipment, are often made using zinc casting due to its excellent corrosion resistance.
4. Building and Construction: Zinc casting is popular in the building and construction industry for producing architectural hardware as well as lighting fixtures.
Zinc Casting vs. Other Casting Techniques
Compared to other casting techniques such as aluminum die casting and sand casting, zinc casting has the following advantages:
1. Superior Surface Finishing: Zinc casting produces smoother and finer surface finishes compared to other casting techniques.
2. Better Tolerance: Zinc casting can achieve dimensional accuracy of up to 0.005 mm, which is more precise than other techniques like sand casting.
3. Higher Strength: Zinc alloys have higher strength-to-weight ratios, making them stronger and more durable than other casting materials like aluminum.
In conclusion, zinc casting is a manufacturing process that offers unique advantages that make it an attractive choice across various industries. Its superior surface finishing, better tolerance, malleability, corrosion resistance, and low cost make it an ideal choice for manufacturers that need to produce high-quality and complex parts. Zinc casting holds a promising future in the manufacturing industry, and with the continuous technological advancement of this process, we can expect to see more innovative applications of this technique.